Im Mercedes-Benz Technology Center (kurz: MTC) in Sindelfingen steht ein zukunftsweisendes Zentrum für die Entwicklung von Elektrofahrzeugen: das Electric Software Hub (ESH). Seit seiner Eröffnung im Jahr 2022 spielt das ESH eine entscheidende Rolle bei der Entwicklung der neuen Elektroauto-Einstiegsmodelle von Mercedes-Benz, wie das neue CLA Coupé (C174) Das Besondere an diesem Hub ist die Bündelung von Software, Hardware, Systemintegration und Testing an einem einzigen Standort. Dadurch wird sichergestellt, dass alle Fahrzeugkomponenten – von der Software bis zur Hardware – perfekt aufeinander abgestimmt sind und reibungslos zusammenarbeiten. Dies ist von zentraler Bedeutung für die effiziente Entwicklung und die Qualitätssicherung der Fahrzeuge.
Die Struktur des Electric Software Hub
Das ESH ist in mehrere Bereiche unterteilt, die jeweils eine spezifische Funktion im Entwicklungsprozess übernehmen. In den oberen Stockwerken des Hubs wird der Software-Code erstellt und in einer sogenannten Vor-Integration getestet. Hier werden die ersten Software-Komponenten entwickelt und ihre Interaktionen in einer virtuellen Umgebung überprüft. Ziel ist es, mögliche Fehlerquellen frühzeitig zu identifizieren und zu beheben, noch bevor die Software in das Fahrzeug integriert wird.
Ein wichtiges Testverfahren im ESH ist die „Hardware-in-the-Loop“ (HIL)-Simulation, bei der physische Hardware-Komponenten mit einer simulierten Fahrzeugumgebung verbunden werden. Diese Methode ermöglicht es den Entwicklern, die Interaktionen zwischen Software und Hardware in einer kontrollierten Umgebung zu überprüfen. Dabei werden nicht nur die Software-Algorithmen getestet, sondern auch die reale Hardware wie Steuergeräte und Sensoren in das Testsetting integriert.
Digitale Erprobungsfahrt: Simulation von Fahrerprobungen
Ein weiteres innovatives Feature des ESH ist die „Digitale Erprobungsfahrt“. In einem speziellen Labor des Hubs wird das Verhalten eines Fahrzeugs in einer vollständig simulierten Umgebung getestet. Dies ermöglicht es den Ingenieuren, die Leistung und das Verhalten eines Fahrzeugs in verschiedenen Szenarien zu erproben – ohne dass ein physisches Fahrzeug notwendig ist. Das virtuelle Fahrzeug wird dabei auf der Grundlage von realen Fahrdaten gesteuert und bewegt sich in einer simulierten Umwelt, die Bedingungen wie Straßenbeschaffenheit, Wetter und Verkehrssituation nachbildet. Dies bietet eine enorme Zeitersparnis, da die Tests ohne den Aufwand einer realen Fahrprobe durchgeführt werden können und dennoch genauso präzise sind.
High-Tech-Testeinrichtungen für reale Fahrzeugerprobungen
Im Erdgeschoss des ESH befinden sich zahlreiche hochmoderne Testeinrichtungen, die speziell entwickelt wurden, um verschiedene Fahrzeugkomponenten unter realistischen Bedingungen zu prüfen. Zu den wichtigsten Teststandorten zählt der Full-Vehicle-System-Prüfstand (FVS). Dieser Prüfstand ist ein besonderes Highlight des Hubs, da er es ermöglicht, ein Fahrzeug im Prinzip ohne Karosserie, aber mit allen wichtigen Bauteilen, zu testen. Der FVS kombiniert zwei entscheidende Systemkomponenten: den Hochvolt-Antriebsstrang, der Elektromotoren und Batterien umfasst, sowie das 12-Volt-Bordnetz, das für weniger energieintensive Fahrzeugfunktionen wie Beleuchtung und Bordelektronik verantwortlich ist. Beide Systeme werden in einer offenen Struktur getestet, sodass alle Teile des Fahrzeugs zugänglich und problemlos austauschbar sind.
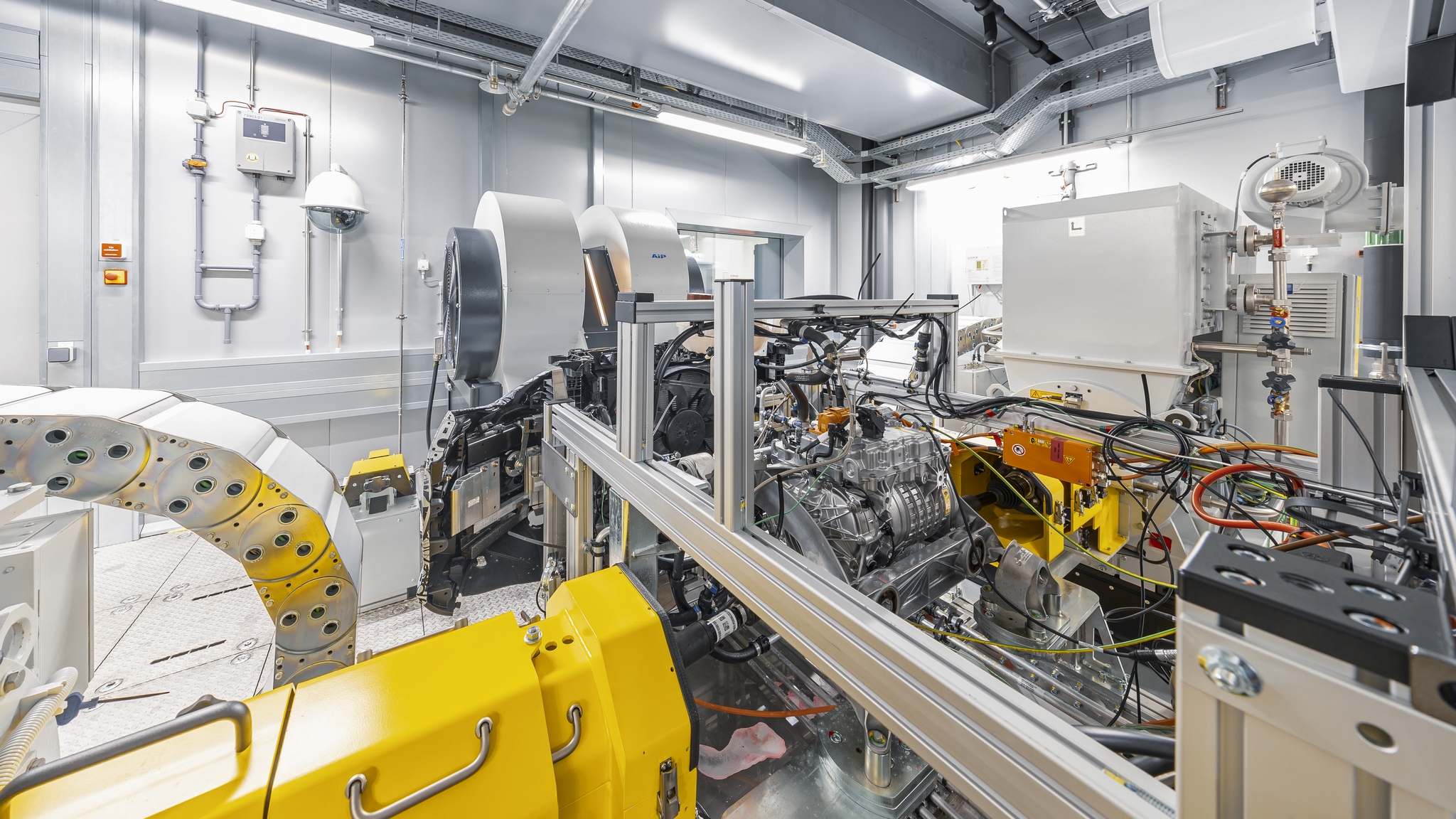
Im FVS kommen auch Fahrroboter zum Einsatz, die auf dem Fahrersitz der Fahrzeugtestaufbauten sitzen und vorgegebene Testfahrten automatisiert durchführen. Ein solcher Fahrroboter, genannt „James“, kann beispielsweise realistische Streckenprofile nachfahren, die aus echten Fahrerprobungen stammen. Dies ermöglicht es den Ingenieuren, die Fahrzeugfunktionen und -komponenten, wie Steuergeräte und Sensoren, unter realitätsnahen Bedingungen zu überprüfen und zu optimieren. Besonders vorteilhaft ist, dass vor Serienproduktion alle relevanten Komponenten, einschließlich Software-Updates, getestet und gegebenenfalls angepasst werden können. Auf diese Weise kann bereits zu einem sehr frühen Zeitpunkt der Entwicklung die Effizienz und Interaktion der Hardware- und Software-Komponenten getestet werden.
Der Fahrzeug-Antriebsstrangprüfstand (F-ATS)
Neben dem FVS gibt es im ESH auch den Fahrzeug-Antriebsstrangprüfstand (F-ATS). Dieser Prüfstand ermöglicht es, den gesamten Antriebsstrang eines Elektrofahrzeugs – vom Elektromotor bis hin zur Batterie – unter extrem realistischen Bedingungen zu testen. Der F-ATS ist mit einer automatisierten Steuerung ausgestattet, die es ermöglicht, komplexe Fahrmanöver und Tests in unterschiedlichen Klimazonen zu simulieren. Auch hier kommt wieder der Fahrroboter „James“ zum Einsatz, der gezielte Manöver in verschiedenen Fahrsituationen durchführen kann. Mit der R2R-Regelung (Road to Rig) können die realen Fahrsituationen aus der Praxis auf den Prüfstand übertragen werden, wodurch die Entwicklung von Elektrofahrzeugen noch präziser und schneller voranschreitet.
Integration von Software-Updates und Release-Hüben
Ein weiterer entscheidender Vorteil des ESH ist die Möglichkeit, neue Software-Versionen – sogenannte Release-Hübe – zu testen. Diese Updates, die während des Entwicklungsprozesses regelmäßig durchgeführt werden, können direkt im FVS und anderen Prüfständen aufgespielt werden. So lassen sich neue Software-Iteration auf ihre Funktionalität und Effizienz testen, bevor sie in die Serienproduktion des Fahrzeugs übernommen werden. Diese Möglichkeit, die Software in einer realitätsnahen Testumgebung zu überprüfen, gewährleistet, dass alle Komponenten – von der Fahrzeug-Software bis hin zur Hardware – stets auf dem neuesten Stand sind und perfekt miteinander harmonieren.
Effizienz und Qualität durch gebündelte Expertise
Der Electric Software Hub von Mercedes-Benz stellt eine bahnbrechende Entwicklung in der Fahrzeugentwicklung dar. Durch die Kombination von Softwareentwicklung, Hardwaretests und Systemintegration an einem einzigen Standort wird der gesamte Prozess der Fahrzeugentwicklung optimiert. Dank innovativer Testmethoden wie der „Digitalen Erprobungsfahrt“, der „Hardware-in-the-Loop“-Simulation und hochmodernen Prüfständen können Ingenieure alle Komponenten eines Fahrzeugs frühzeitig testen und aufeinander abstimmen. Dies führt zu einer signifikanten Beschleunigung des Entwicklungsprozesses und einer höheren Qualität der Fahrzeuge, die letztlich den Fahrern zugutekommt. Das ESH bietet Mercedes-Benz einen klaren Wettbewerbsvorteil auf dem Markt der Elektrofahrzeuge, indem es eine präzise, effiziente und zukunftsweisende Fahrzeugentwicklung ermöglicht.
Bilder: Mercedes-Benz Group AG